Application
Use pressure mapping technology to fine-tune nip roll settings, reduce waste, enhance print quality, and boost production efficiency.
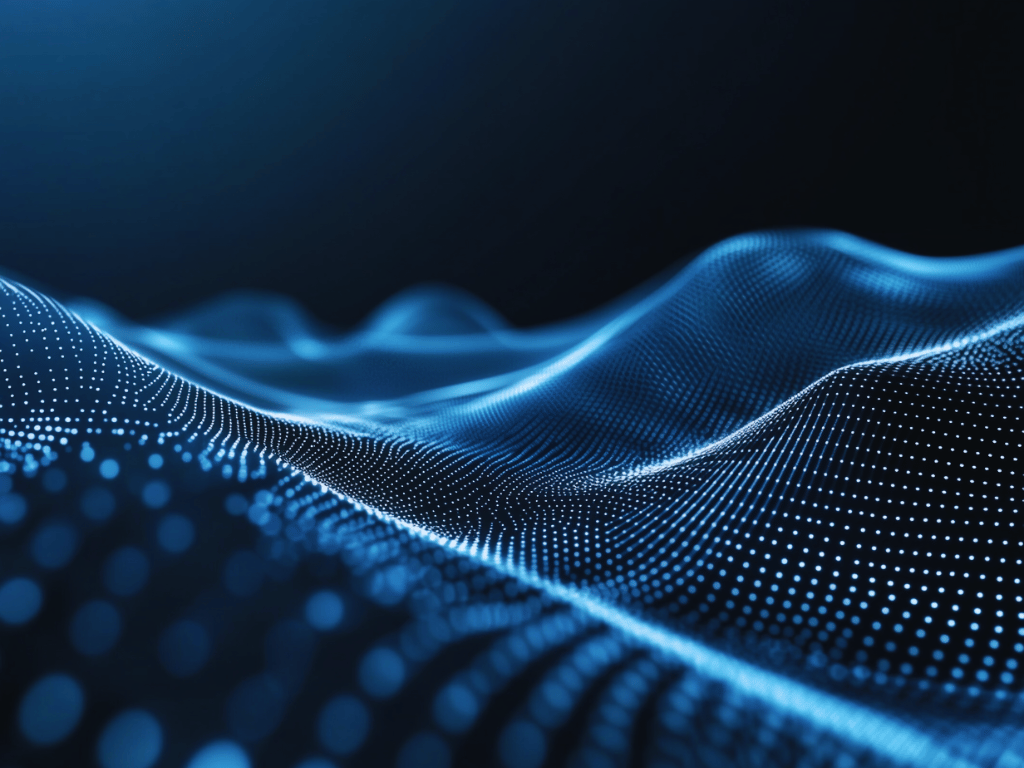
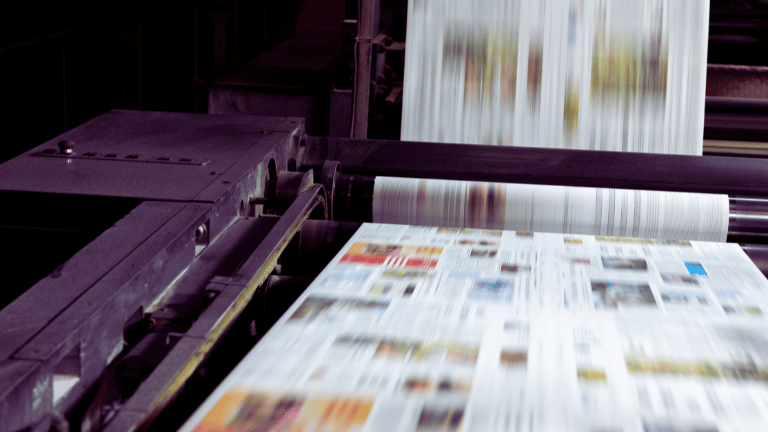
Pressure Mapping for Nip Roll Optimization : Improve Print Quality & Efficiency
Introduction
In high-speed industrial printing and lamination, nip roll pressure settings directly influence output quality, equipment longevity, and process stability. As materials become more sensitive and production speeds increase, traditional pressure calibration methods fall short. Pressure mapping technology enables engineers to visualize contact force in real time—delivering actionable data for consistent, high-efficiency operations.
Why Nip Roll Pressure Matters
Incorrect pressure leads to predictable yet costly issues:
- Overpressure → substrate damage, ink bleeding, or layer deformation
- Underpressure → poor ink transfer, misalignment, or adhesion failure
- Imbalanced pressure → web tension inconsistencies, roll skew, and mechanical wear
These problems translate into quality defects, increased downtime, and higher maintenance costs. In continuous print lines, consistent nip pressure is essential for maximizing throughput and minimizing disruptions.
How Pressure Mapping Improves Performance
Unlike manual or static testing, pressure mapping systems provide high-resolution, real-time feedback on actual nip surface conditions. Key benefits include:
🔸 Visualized pressure distribution across the full contact surface
🔸 Detection of subtle irregularities for micro-scale adjustment
🔸 Data logging and integration with MES/SPC systems for quality traceability
🔸 Precision-guided tuning, supporting zonal or bilateral pressure correction
This data-driven approach improves not only initial calibration but also ongoing monitoring, enabling predictive maintenance and smarter process control.
Application Fields and Practical Value
Pressure mapping systems add measurable value across multiple sectors:
🔹 Packaging: Ensure seal strength and print alignment on films and cartons
🔹 Electronics: Optimize bonding accuracy in flexible circuits and display layers
🔹 Textile & Coating: Improve embossing, surface uniformity, and material consistency
🔹 Renewables: Stabilize thin-film pressure in solar panel layer transfer for better conductivity and durability
Conclusion
By implementing pressure mapping into nip roll operations, manufacturers gain deeper process insight, faster response to anomalies, and significantly improved production consistency. Moving beyond guesswork and toward data-guided calibration allows for higher efficiency, better product quality, and reduced operational cost over time.
Latest Insights
Collaboration Begins Here.