Application
Discover how pressure mapping with FSR grids helps validate EV battery designs, improving stability, durability, and assembly quality.
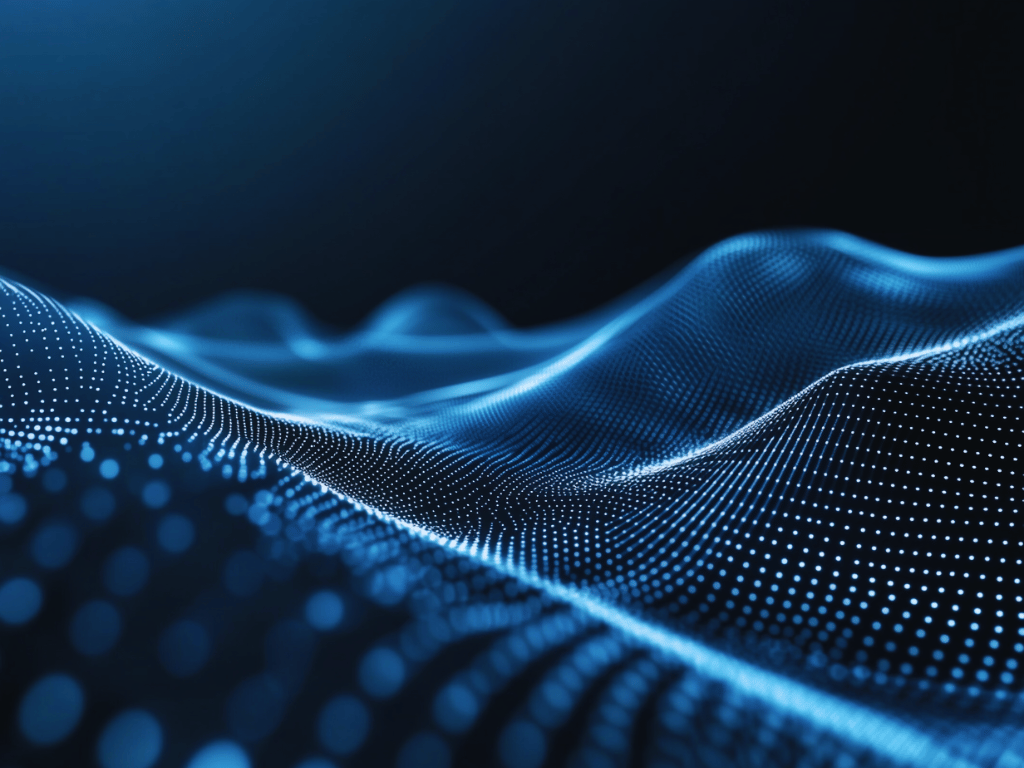
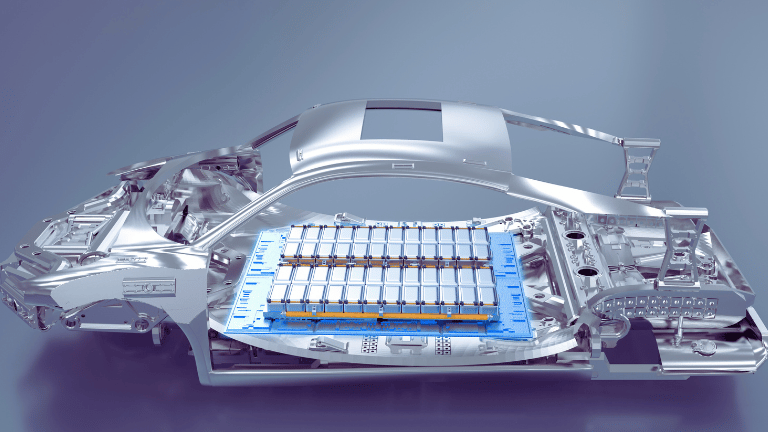
Understanding Pressure Mapping and Validation in EV Battery Design with FSR Technology
Introduction
As electric vehicles (EVs) move into mass production, battery design challenges are becoming more complex. It's not just about packing in more energy or charging faster anymore—how the battery holds up under mechanical stress is just as important.
One area that's starting to get more attention is pressure behavior inside the battery pack. Pressure changes can affect how tightly cells fit together, how heat moves through the pack, and even how well seals and structures hold up over time.
To support design validation, some teams are starting to use pressure mapping with custom-designed Force Sensing Resistor (FSR) grids. These flexible sensing layers can be temporarily added during development and testing to visualize where pressure is building up or shifting. Even though these sensors aren't meant to stay inside the final battery, they can offer valuable insights during early validation phases.
Design and Validation Insights Using Pressure Mapping
1. Pressure Shifts During Charge Cycles
As lithium-ion cells charge and discharge, they expand and contract slightly. These movements can seem small, but over time, they create internal stresses that can cause:
- Shifting or misalignment between cells
- Extra pressure against the battery casing
- Changes in thermal pathways that affect cooling
Installing a thin FSR grid inside prototype modules during validation helps engineers monitor subtle pressure changes under real-world conditions.
This supports design improvements such as:
- Adjusting casing flexibility or reinforcement
- Improving thermal management strategies
- Catching early signs of mechanical stress before finalizing designs
Instead of relying only on simulation, teams can validate how pressure actually behaves during operation.
2. Environmental Durability Testing
In real-world driving, battery packs must survive impacts, vibration, and environmental stress like water spray and aerodynamic forces. Over time, these external pressures can lead to:
- Cracks or deformations in the battery housing
- Water or dust intrusion into seals
- Stress fractures in structural parts
During environmental validation tests, FSR mats can be used to map pressure distribution caused by simulated conditions like road debris impact or high-pressure washing.
This helps engineers:
- Reinforce areas vulnerable to mechanical fatigue
- Choose stronger or more flexible housing materials
- Design better protection features to improve long-term durability
Mapping pressure during validation gives clearer guidance for strengthening battery pack designs.
3. Uniform Compression During Module Assembly
Even pressure during battery module assembly is critical for long-term performance. Uneven compression can cause:
- Poor electrical contact between cells
- Increased risk of damage from vibration or thermal cycling
- Inconsistent module quality
By using FSR layers during early assembly validation, manufacturers can monitor how evenly compression is applied across all cells.
This enables:
- Fine-tuning of press-fit equipment
- Reducing risks of cell deformation or assembly defects
- Building greater consistency into mass production setups
Real-world validation of assembly pressure improves both quality and reliability.
Conclusion
Although FSR grids are usually removed before final battery assembly, their role during design and validation is crucial. Mapping pressure behavior early—during charging cycles, environmental tests, and stacking processes—gives engineers the real-world feedback needed to build stronger, safer, and more reliable EV battery packs.
As EV designs continue to evolve toward higher energy densities and tighter form factors, pressure mapping during validation will become an increasingly valuable tool for ensuring success beyond the lab and onto the road.
Latest Insights
Collaboration Begins Here.